Building Statistics
North Hills Tower IV
North Hills Tower IV is a large-scale commercial construction project developed by Kane Realty Corporation in Raleigh, North Carolina. It is a 20-story building, which includes a 9-floor parking garage, 11 floors of office space built on top, and a ground floor with retail space. Located in Midtown Raleigh, Tower IV will be the largest building in the rapidly growing development area known as North Hills.
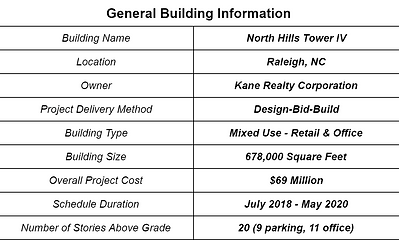
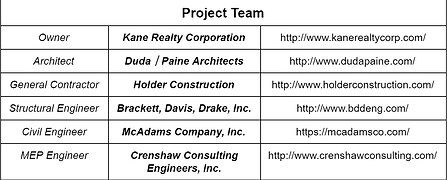
Architecture
North Hills Tower IV is currently only designed to be a core/shell building, with the tenant buildout coming at a later date. It is mostly a cast-in-place concrete structure, featuring a cantilevered roof section. Eleven floors of office space is to be built on top of a 9-floor parking garage. The ground floor will be designated for retail space. There is also a mechanical penthouse located on the roof.

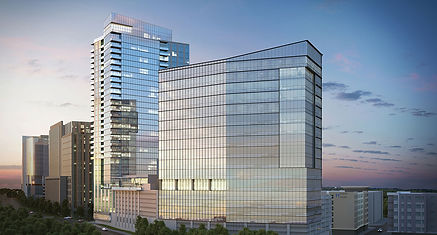
Codes and Zoning
This project abides by the 2012 North Carolina State Building Code (NCSBC), which is indicated in the Construction Documents. One major zoning concern mentioned by Holder Construction was the restrictions on tower crane heights. The Federal Aviation Administration has strict regulations on how tall tower cranes can be while on site, due to the proximity of the Raleigh-Durham International Airport.
Enclosure
The building facade for North Hills Tower IV consists of both a glass curtain wall system and metal panel wall system. The glass curtain wall is aluminum framed, with vision glass and glass infill panels. The vision glass portions are insulated glass units, meaning they have two layers of glass, filled with argon in between. The glass infill panels are backed with mineral board insulation. The metal panel wall system is composed of Metal Composite Material (MCM) rainscreen panels. This system is framed by aluminum and is backed by a vapor retarder, sheathing, and steel studs.
The roofing system used in this building was a thermoplastic polyolefin (TPO) system. This is a single ply membrane that can either be adhered or mechanically attached. The membrane is applied on the cast-in-place slab, with board insulation in between.

Pictured left to right: Glass Curtain Wall System, MCM Wall Panel System, TPO Roofing System.
Sustainability
While there are no major sustainability features in the design (i.e. a green roof or something similar), the project team is seeking to achieve a LEED Gold certification. In order to achieve the Gold rating, the United States Green Building council requires between 60-79 points to be earned upon completion.

Construction
The contract that North Hills Tower IV utilizes is a CM at Risk delivery system. The general contractor was involved early in the design process to assist the owner, and a GMP of $69 Million was agreed upon They then completed the work on their own, hiring subcontractors for each trade.
The method of constructing the cast in place core and shell structure includes utilizing a tower crane to lift concrete pumps up the building so that slab and structural members can be poured. This process starts from the bottom and goes vertically up. During the foundation installation, work begins at the lowest elevation of the building and moves upward.
Electrical
The electrical system used in the project includes a fuel-run generator that features a minimum 2,600 KVA starting capacity. This generator also has the capacity to operate at full load for at least 10.67 hours, and passes power on to the rest of the building by way of conduit running underneath the ground floor slab.
Mechanical
The mechanical design for the tower utilizes a rooftop penthouse to provide ventilation to the building. This penthouse includes both cooling towers and air handling units. Roof exhaust fans eject used air out of the building. The heat production for the ground retail space is provided by a water sourced heat pump, which is located on the ground floor. As for the rest of the building, the main source of heat comes from electric heaters. The air handling units can provide up to 2750 CFM of air.
Structural
The cast-in-place concrete superstructure all hinges on the foundation work, which employs a pile and pile cap system. Both 36" diameter and 24" diameter piles are used, and are installed using a CFA auger rig. Both pile types have a design concrete strength of 5,000 psi. Earth formed grade beams are installed as well, with a thickness of 1'-4". Finally, due to leaning columns in the superstructure above, tie beams must also be used in the foundation system. These tie beams have a thickness of 1'-6" and lie under the 5" slab on grade.
Fire Protection
The fire suppression system used in Tower IV is a wet system with a pump. A wet system is one that employs automatic sprinklers throughout the suppression system, with water ready to be dispensed once the alarm is tripped. The pump that provides pressure for the water is located on the ground floor of the building.